How intelligent industrial automation enhances safety, efficiency and resilience
The push for robustness continues in digital hydraulics, where an LQR and H-infinity-based control strategy was tested for regulating axial piston pump speed. The H-infinity controller was especially effective in rejecting external disturbances, making it ideal for hydraulic systems where real-world volatility is high.
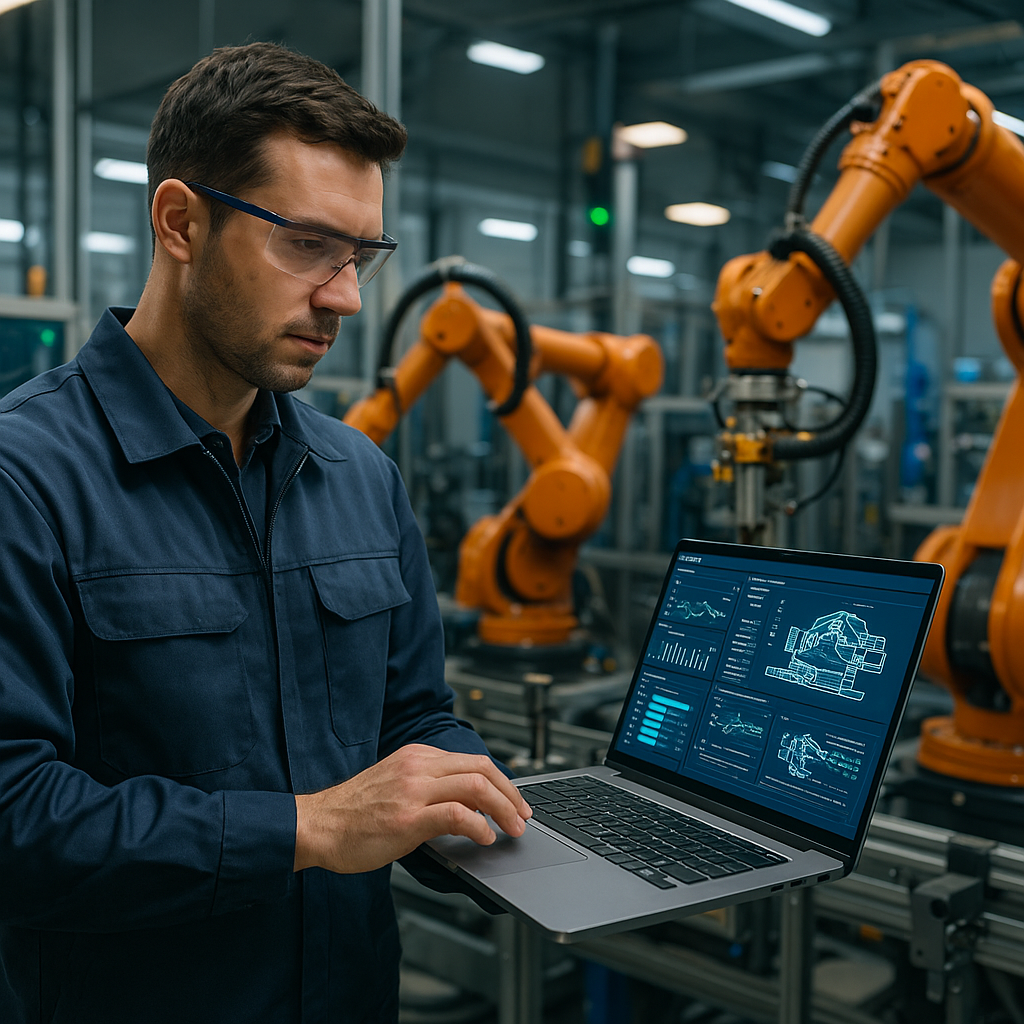
Industrial operations are undergoing a profound transformation, driven by mounting demands for sustainability, digital integration, and operational efficiency. A new editorial spotlights groundbreaking research that is reshaping the field of process control and monitoring. Published in Processes, the piece “Advancing Industrial Automation: Highlights from Recent Research” demonstrates critical advancements pushing automation technologies to the forefront of modern industry.
The featured research spans multiple fields and industries, highlighting innovations in robust control, dynamic optimization, fault detection, and predictive analytics. The editorial synthesizes advancements that show how artificial intelligence, digital twins, and intelligent sensor technologies are leading a paradigm shift in how industrial systems operate, adapt, and self-correct.
How are new control strategies enhancing industrial resilience?
The editorial shows the application of advanced control strategies to address operational variability and uncertainty. Among the highlighted contributions, several studies explore how process systems can better respond to fluctuating inputs and external disturbances using state-of-the-art control theory.
One study introduces a dynamic optimization model for green methanol production that allows flexible adjustments to hydrogen supply interruptions through feed-forward control systems. This model is a step forward in integrating sustainability goals with real-time production constraints. Another paper offers a robust fuzzy control framework for nonlinear descriptor systems using Takagi–Sugeno modeling, which ensures system stability even in the face of modeling uncertainties without inducing noncausal system behavior.
The push for robustness continues in digital hydraulics, where an LQR and H-infinity-based control strategy was tested for regulating axial piston pump speed. The H-infinity controller was especially effective in rejecting external disturbances, making it ideal for hydraulic systems where real-world volatility is high.
Together, these studies demonstrate a shift from reactive to proactive control, signaling an era where systems can preemptively adapt to changing conditions without human intervention. This ability to ensure performance stability despite variable conditions is essential for energy-intensive and sustainability-driven sectors.
What role does fault detection play in intelligent automation?
Secondly, the editorial focuses on the growing importance of fault detection and diagnostics as cornerstones of modern industrial automation. Advanced fault detection ensures not only continuity of operations but also plays a critical role in reducing energy waste, equipment wear, and operational downtime.
Among the featured work is a digital twin-based leak detection method for hydraulic systems. This technique integrates real-time sensor data with genetic algorithm optimization to identify leakage events with high accuracy. The use of digital twins as virtual replicas of physical systems represents a powerful move toward predictive maintenance.
Complementing this, a study on fluidized bed boilers introduced a novel fault detection method based on shared nearest neighbor clustering. It was found to outperform more traditional techniques such as principal component analysis and independent component analysis, marking a leap in early-stage fault recognition.
A further advancement was introduced in the context of diesel engine systems, where data-driven techniques using Hammerstein models were applied to detect oscillatory faults. These models rely on identifying subtle behavioral anomalies, offering a scalable approach to engine monitoring.
This body of work reflects a broader trend toward integrating AI and data science into industrial diagnostics. Fault detection is no longer about post-failure analysis, it is about real-time surveillance and actionable prediction, enabling smarter and safer systems.
Can optimization and AI technologies meet the demands of Industry 4.0?
The editorial also explores the integration of optimization models and AI to meet the complex demands of Industry 4.0. This includes case studies in sectors such as biofuels, mining, and petrochemicals, where data scarcity and operational constraints often hinder innovation.
One study applied few-shot learning and long short-term memory networks to optimize biodiesel production in environments with limited historical data. This approach combines the adaptability of machine learning with the reliability of established process models, ensuring operational efficiency without requiring vast datasets.
Another contribution developed a computer vision system based on YOLOv8 to enhance safety in coal transport monitoring. This system could detect solidification risks in real time using fluorescence signals, enabling rapid intervention in hazardous settings.
Further advancements were presented in real-time chatter detection during machining operations. A hybrid model using denoising autoencoders and bidirectional LSTM layers was able to detect harmful vibrations and recommend corrective actions. This has direct implications for manufacturing, where tool life and product precision are paramount.
In petrochemical safety, a new risk-based inspection method that integrates integrity operating windows was introduced. This dynamic approach allows continuous evaluation of failure risks based on operational changes, rather than fixed inspection intervals, thereby enhancing both safety and cost-efficiency.
- FIRST PUBLISHED IN:
- Devdiscourse