Digital twin and metaverse technologies redefine workplace safety in manufacturing
The integration of DT and IM tools enables a dynamic, real-time replication of physical manufacturing environments in digital spaces. A Digital Twin simulates machinery, systems, and even worker movement to detect inefficiencies, anomalies, or risks before they materialize. When coupled with Industrial Metaverse components, such as Extended Reality (XR), Virtual Reality (VR), and Augmented Reality (AR), these tools evolve into interactive, immersive platforms for safety visualization, simulation, and training.
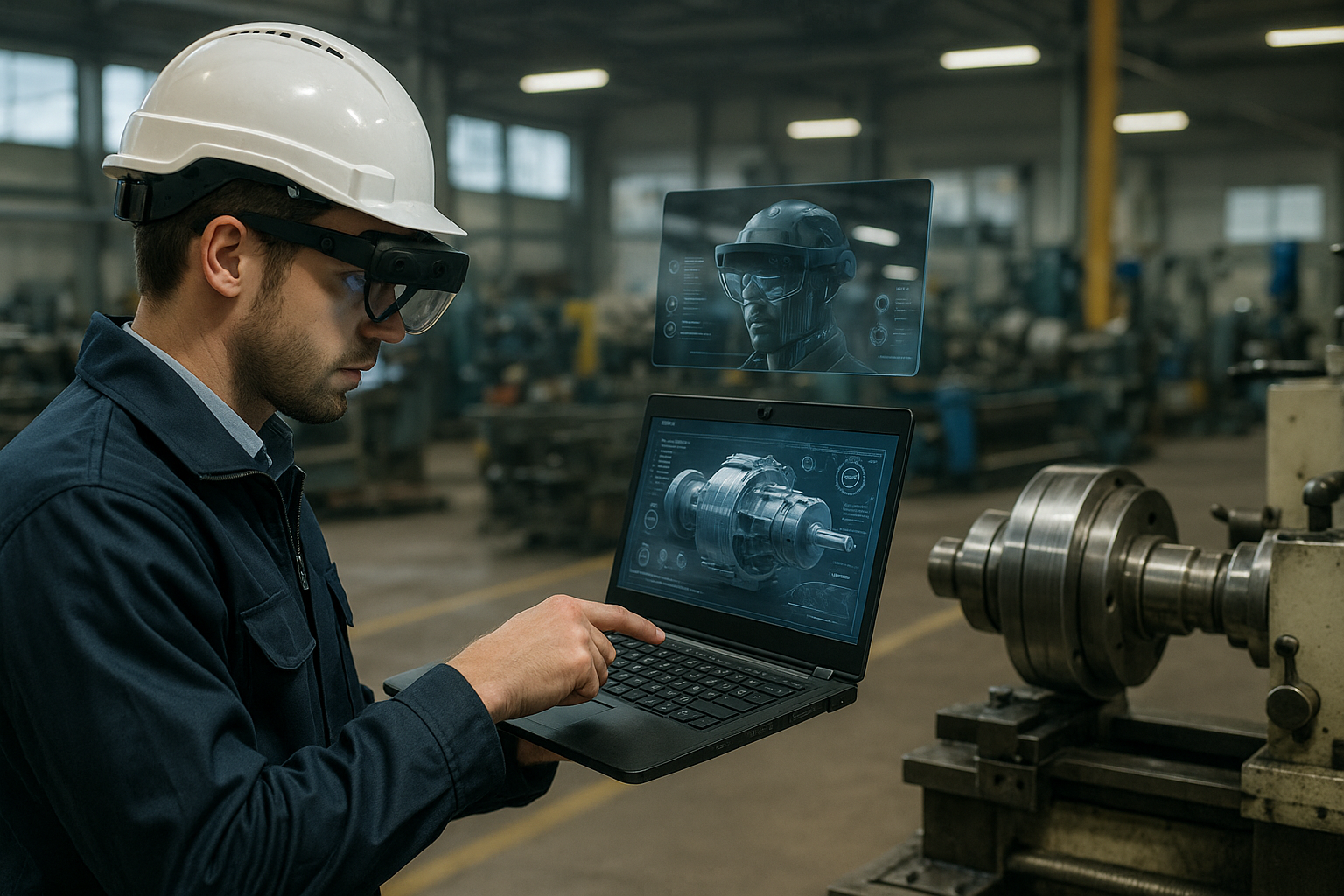
Amidst the shift from Industry 4.0 to Industry 5.0, manufacturers are facing a dual imperative: improve operational efficiency while protecting human health. A new study examines how two transformative technologies, Digital Twin (DT) and the Industrial Metaverse (IM), are reshaping occupational health and safety (OHS) standards in manufacturing environments.
A paper published in Applied Sciences, titled "Exploring the Role of Digital Twin and Industrial Metaverse Technologies in Enhancing Occupational Health and Safety in Manufacturing, offers a timely and comprehensive analysis of how virtual technologies can reduce workplace accidents, improve training, and enhance real-time hazard response systems. Based on a systematic review of 75 peer-reviewed articles guided by PRISMA methodology, the research provides a strategic blueprint for integrating immersive digital solutions to proactively safeguard workers.
How do digital twin and industrial metaverse technologies enhance safety?
The integration of DT and IM tools enables a dynamic, real-time replication of physical manufacturing environments in digital spaces. A Digital Twin simulates machinery, systems, and even worker movement to detect inefficiencies, anomalies, or risks before they materialize. When coupled with Industrial Metaverse components, such as Extended Reality (XR), Virtual Reality (VR), and Augmented Reality (AR), these tools evolve into interactive, immersive platforms for safety visualization, simulation, and training.
According to the study, this hybrid ecosystem enhances OHS in several ways. First, real-time data generated from Internet of Things (IoT) sensors and Cyber-Physical Systems (CPS) can be visualized and analyzed for predictive maintenance, exposure tracking, and incident anticipation. Second, through the Industrial Metaverse, safety protocols can be tested, refined, and taught in realistic virtual environments without putting workers at risk.
For example, workers can undergo hazard recognition exercises in a simulated version of their own facility using AR headsets, practicing emergency procedures and identifying safety violations. Simultaneously, supervisors and engineers can use the Digital Twin environment to analyze fatigue patterns, thermal stress, and equipment interaction risks, enabling immediate intervention when thresholds are breached.
The study highlights how the fusion of these technologies transforms safety from a reactive obligation to a proactive, strategic function. Safety is no longer confined to manuals or isolated drills; it becomes embedded in the continuous operation of a smart, responsive factory.
What are the key enabling technologies driving this transformation?
At the heart of this evolution lies a suite of interconnected digital technologies that together support a resilient safety architecture. These include:
- Extended Reality (XR): Combines AR, VR, and Mixed Reality (MR) to create immersive environments for training and incident rehearsals.
- Collaborative Robots (Cobots): Integrated into Digital Twin systems to monitor and learn from human-robot interaction risks.
- Artificial Intelligence (AI): Processes real-time data to identify patterns and anomalies associated with hazardous conditions.
- Cyber-Physical Systems (CPS): Sync physical machines with digital platforms to provide constant feedback and control over safety-critical systems.
- IoT Devices and Wearables: Collect biometric and environmental data for real-time safety monitoring.
The convergence of these technologies enables manufacturers to develop what the authors call a “Digital Safety Ecosystem”, a self-learning, responsive environment that evolves based on behavioral data and contextual inputs. This not only reduces time lost to accidents but also aligns safety strategies with broader operational goals.
The study also highlights the role of Digital Twin and Metaverse platforms in meeting sustainability and well-being objectives aligned with the United Nations’ Sustainable Development Goals (SDGs), particularly those concerning decent work and industry innovation.
What are the challenges and future directions for implementation?
Despite the promise, widespread implementation of DT and IM technologies in occupational safety is not without challenges. The study outlines several key barriers that industries must address:
- Technical Complexity: Building an integrated system that combines DT, IM, AI, and IoT requires significant technical expertise and robust infrastructure. Small and medium enterprises may find the initial cost and integration effort daunting.
- Cybersecurity and Data Privacy: Real-time monitoring involves sensitive personal and operational data. Without stringent cybersecurity measures, these systems can become vulnerable to breaches or misuse.
- Organizational Resistance: Shifting to immersive safety platforms requires cultural change. Employees accustomed to conventional training methods may resist virtual training tools, especially older workers or those with low digital literacy.
- Standardization Gaps: There is currently a lack of global standards for implementing and evaluating the effectiveness of Digital Twin and Metaverse safety protocols. This slows cross-industry adoption and benchmarking.
The authors recommend that companies begin with pilot implementations focusing on high-risk environments where return on investment is immediate. Strategic partnerships with academic institutions, technology providers, and regulatory bodies can also help build standardized frameworks and accelerate adoption.
They further suggest that ongoing employee education and gradual digital integration are critical for long-term success. Creating user-friendly interfaces and providing continuous support will be necessary to achieve behavioral buy-in and ensure safe engagement with complex digital systems.
- FIRST PUBLISHED IN:
- Devdiscourse